Blade Damage Monitoring
Blade surface damage: Identify turbines requiring attention
Continuously monitor your turbines to detect surface damage at an early stage, preventing minor issues from developing into major failures.
What our :SURFACE HEALTH offers you
Wind turbine damage can occur anytime, even right after an inspection. Without continuous monitoring, you’re operating blindly, risking undetected damage that leads to high costs, extensive maintenance, and reduced performance.
Our :SURFACE HEALTH solution provides continuous rotor blade surface monitoring, detecting damage early to prevent costly disruptions. It also tracks existing issues, alerting you if they worsen. This proactive approach helps you prioritize turbines requiring attention, ensuring optimal performance and minimizing unexpected expenses. Trust :SURFACE HEALTH to safeguard your operations with continuous monitoring and timely alerts.
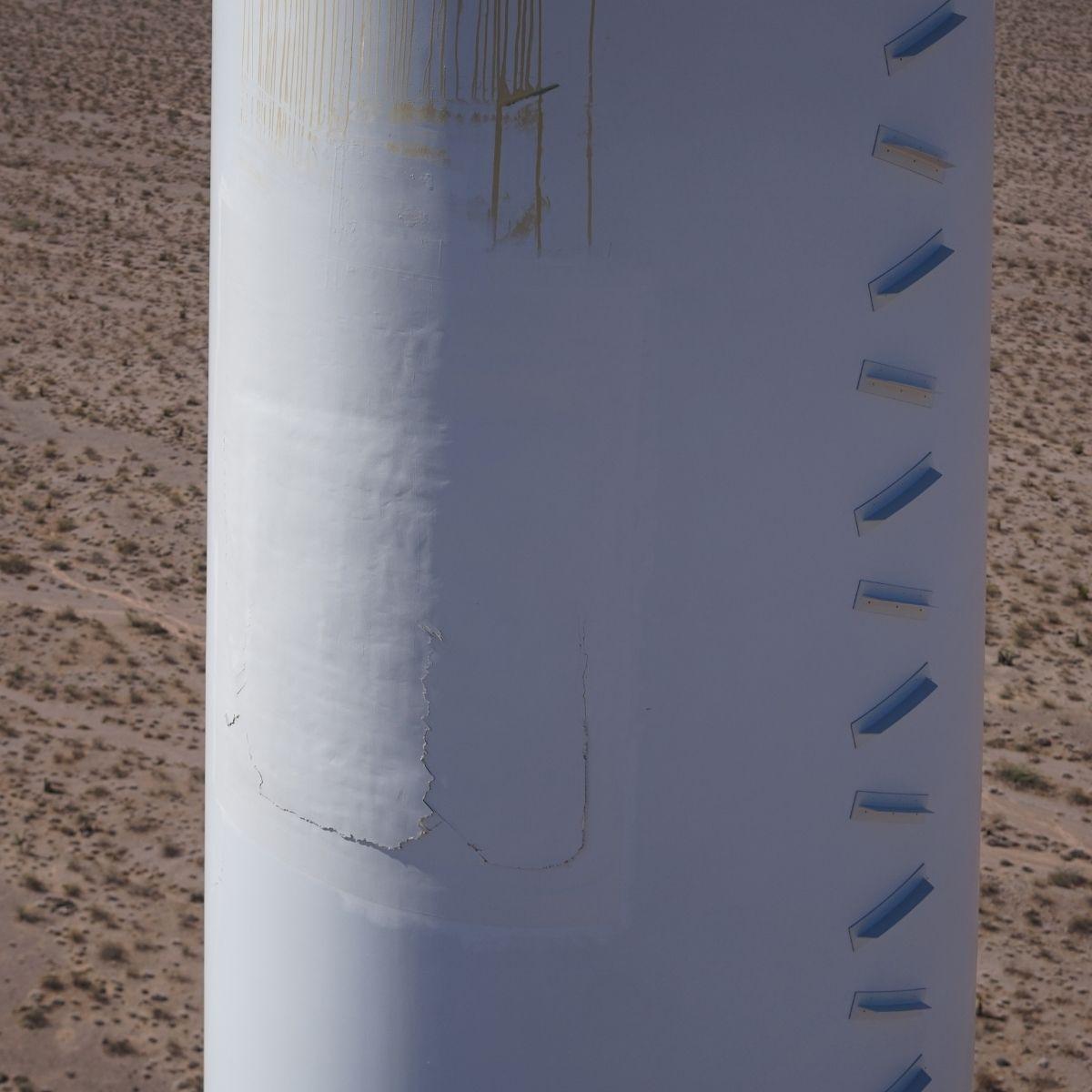
Early detection for optimized repair
Our surface damage detection solution uses acoustic emissions caused by airflow over damage and disturbances to monitor the overall condition and look for trends/emergencies in the surface condition. This enables early damage detection, timely repairs and prevents small problems from developing into critical failures.
Reduce unplanned downtime
Not only does our system allow you to proactively address root causes, it also allows you to prioritize repairs and shutdowns for visual inspections. This reduces interruptions and ensures continuous operation and increased annual energy production (AEP).
Streamline visual inspections
With our monitoring system, you can optimize visual inspections by focusing on the turbines that require your attention. This increases the efficiency of inspections and improves the use of resources.
Our products at a glance
Blade risk
:SURFACE HEALTH - Blade surface damage monitoring
Monitoring surface damage with acoustic sensors, detecting issues like split tips, erosion, cracks, etc.
- Monitoring overall blade condition
- Dashboard access & Notifications
- Training & Support
Stay ahead of repairs: Instant damage detection that saves time and money
Save costs, minimize downtime, and optimize inspections. Catch damage early, cut repair costs, and keep your turbines running smoothly with our fast-install, cost-efficient monitoring system – seamlessly integrated without disrupting OEM contracts.
Want to know when damage occurs?
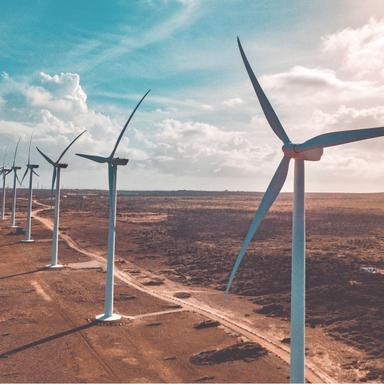
Immediate damage indication
Our system detects damage and changes as soon as they occur. This allows earlier repair when it is much more cost effective.
Effective and cost-efficient monitoring
With affordable prices and flexible terms, our system can be seamlessly integrated into your budget.
Fast and easy installation
Our acoustic surface damage detection system is designed for quick and easy installation, taking less than 10 minutes for steel towers.
Early detection saves costs
The faster damage is detected, the faster you can react to it. This saves time and personnel resources as well as repair costs.
Optimize inspection processes
Regular monitoring of blade health ensures that inspections are carried out based on actual data. By reducing unnecessary and routine inspections, the frequency and efficiency of inspections can be optimized, resulting in cost savings on manpower and resources.
No interference with existing OEM contracts
:SURFACE HEALTH is designed to be easily integrated. It does not interfere with existing OEM contracts.
Don’t miss lightning strikes
Thanks to our lightning protection upgrade, you can easily determine whether your wind turbine has been struck by lightning. The hardware remains unchanged, allowing you to easily expand your monitoring capabilities.
Package tailored to your needs
With our product, surface damage never goes undetected again. (Note: All prices are valid for 2025.)
:SURFACE HEALTH - Blade surface damage monitoring
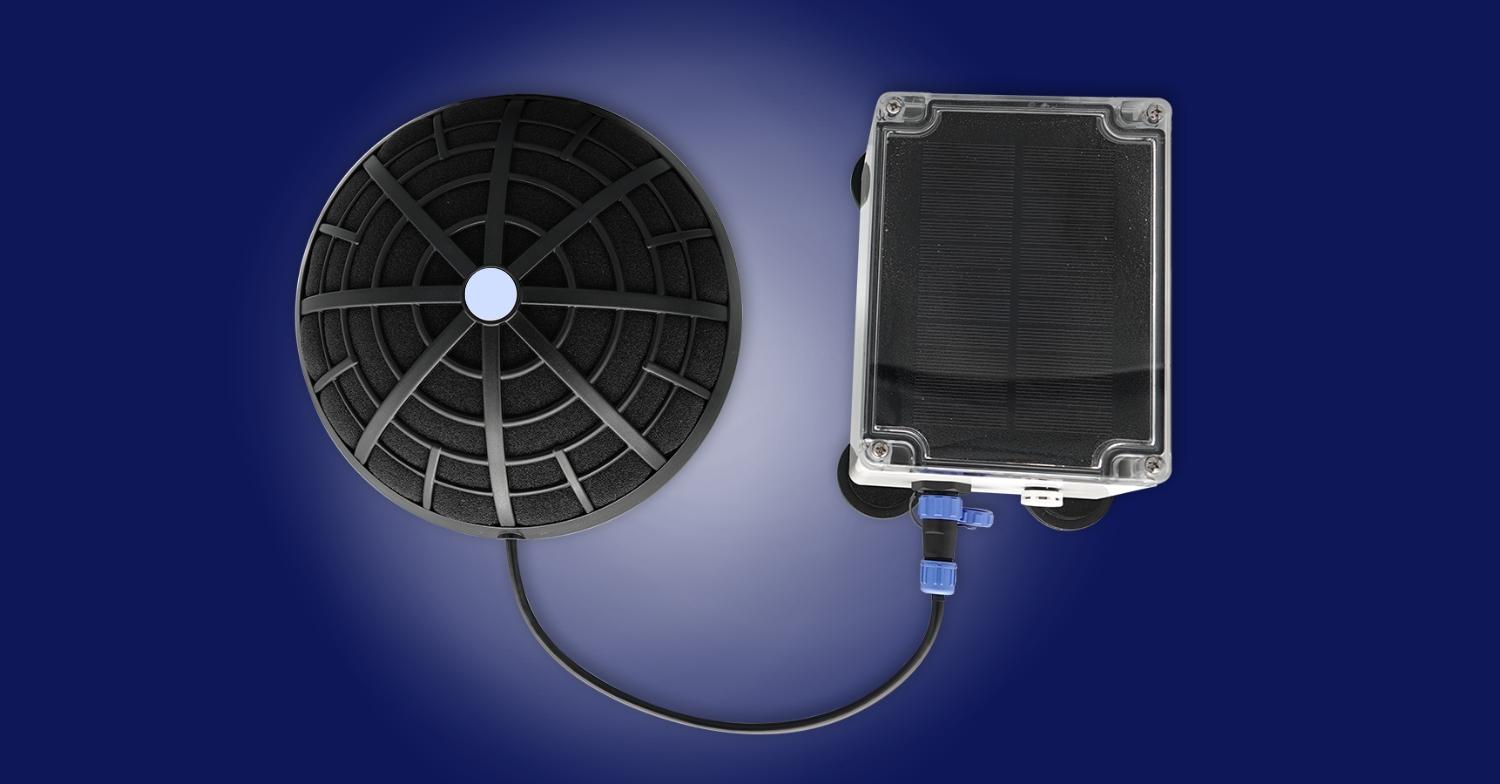
Monitoring surface damage with acoustic sensors, detecting issues like split tips, erosion, cracks, etc.
- Uses the ON-TOWER technology with acoustic sensors
- Is equipped with PCM as receiving unit
- Is mounted on the base of the turbine with magnets or adhesive
- Detects surface damage
- Installed within minutes by your own service team
Cost Overview
Standard
:SURFACE HEALTH
•
Fast and early detection of rotor blade damage
•
Dashboard access & Notifications
•
Training & Support
Package includes
This package contains an Intelligent Listening Sensor (ILS), Power and Communication Module (PCM) and an Interconnecting Cable (IC).
:SURFACE HEALTH starting at
per wind turbine per year
Surface damage common questions
Further information needed?
If you have any questions, our team is always happy to help. Do not hesitate to get in touch with us.