Blade Operation Monitoring
Precision blade heating: Reduce unnecessary power consumption and improve efficiency
Struggling with inefficient blade heating? Inefficient blade heating strategies not only waste energy but also lead to high operational costs and downtime during operation. Optimize your blade heating system and eliminate unnecessary heating cycles.
How precision heating helps you
Ice accumulation on rotor blades and inefficient heating strategies can lead to significant safety risks and increased operational costs. With high-precision ice detection and optimized blade heating control, you can ensure efficient turbine performance even in the harshest winter conditions.
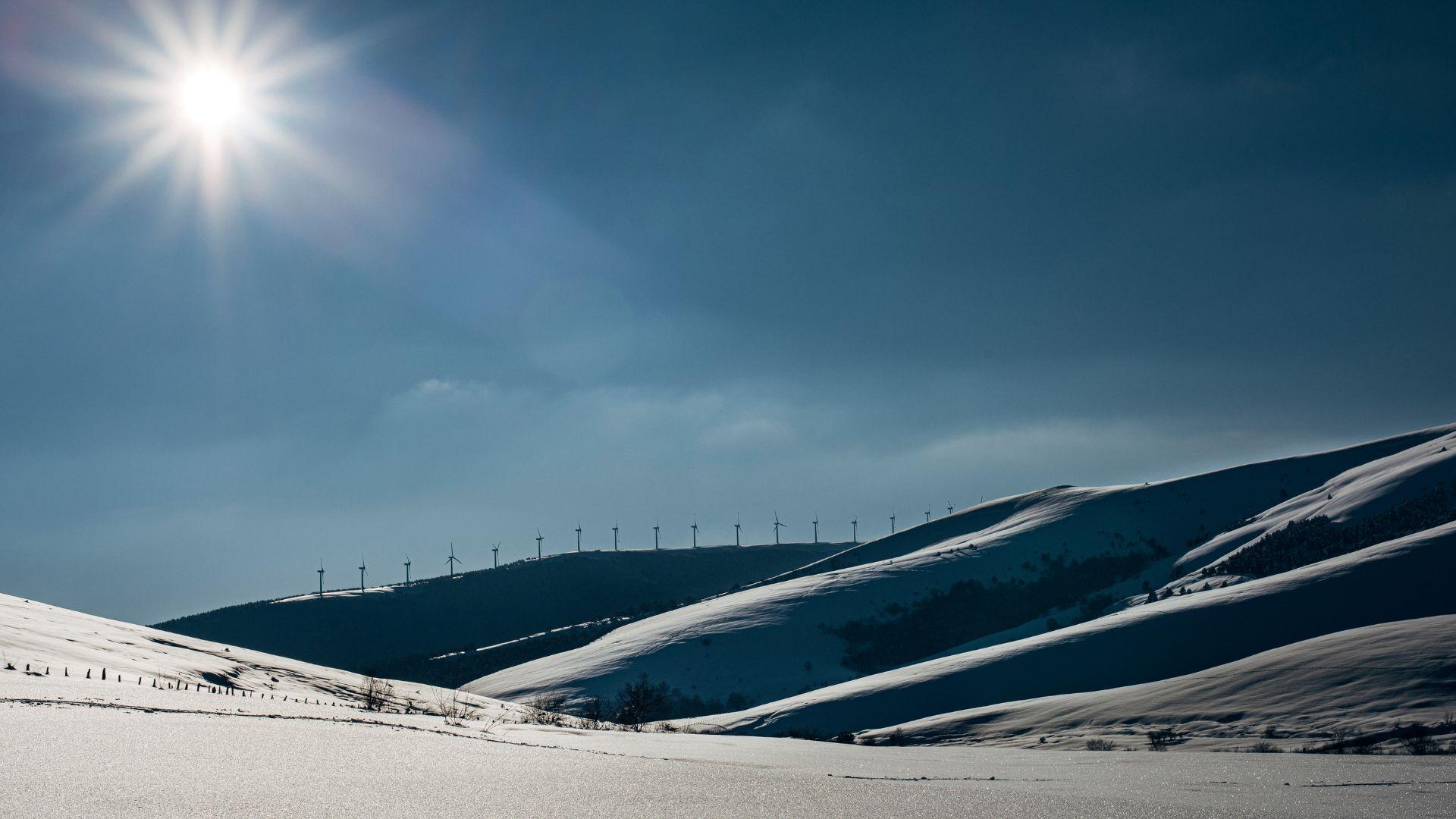
Increase performance
:HEAT uses the new generation of our wireless ON-BLADE technology to measure the surface temperature and ice thickness directly on the blade surface. This enables precise control of the anti-icing system with the optimal timing to ensure ice-free blades at the lowest possible power consumption.
Fully integrated into existing systems
:HEAT is designed for both new installations and retrofits. The standardized interfaces enable seamless and fast integrate into existing turbine control systems.
Real-time monitoring and promptly alerts
Enables operators to track ice formation and heating performance in real-time.
Harsh climate resilience
Designed to perform even in extreme weather conditions, such as in Scandinavian winters.
Our product
Blade Operation Monitoring
:HEAT
ON-BLADE system including temperature and ice detection sensors for efficient blade heating.
Improve your blades heating performance
Optimize your heating and anti-icing performance with our innovative, autonomous wireless blade sensor system to keep blades ice-free while ensuring precise and efficient performance.
Protect your assets from the consequences of inefficient blade heating
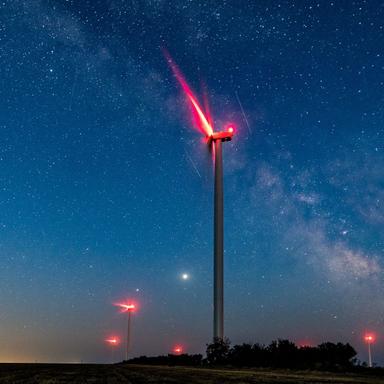
Optimized power consumption
Our advanced precision heating solution minimizes heating-related energy waste without compromising performance.
Maximized turbine uptime
Our technology ensures turbines remain ice-free and ready for operation when energy prices peak.
Blade condition awareness
Gain precise insights into the icing state of your blades and monitor the effectiveness of your heating system in real-time.
Retrofit and easy integration
Our system is designed so that it can be seamlessly integrated into existing wind turbine controllers.
One product for efficient blade heating
To support operators, our product has been designed to optimize the heating performance of the blades. (Note: All prices are valid for 2025.)
:HEAT
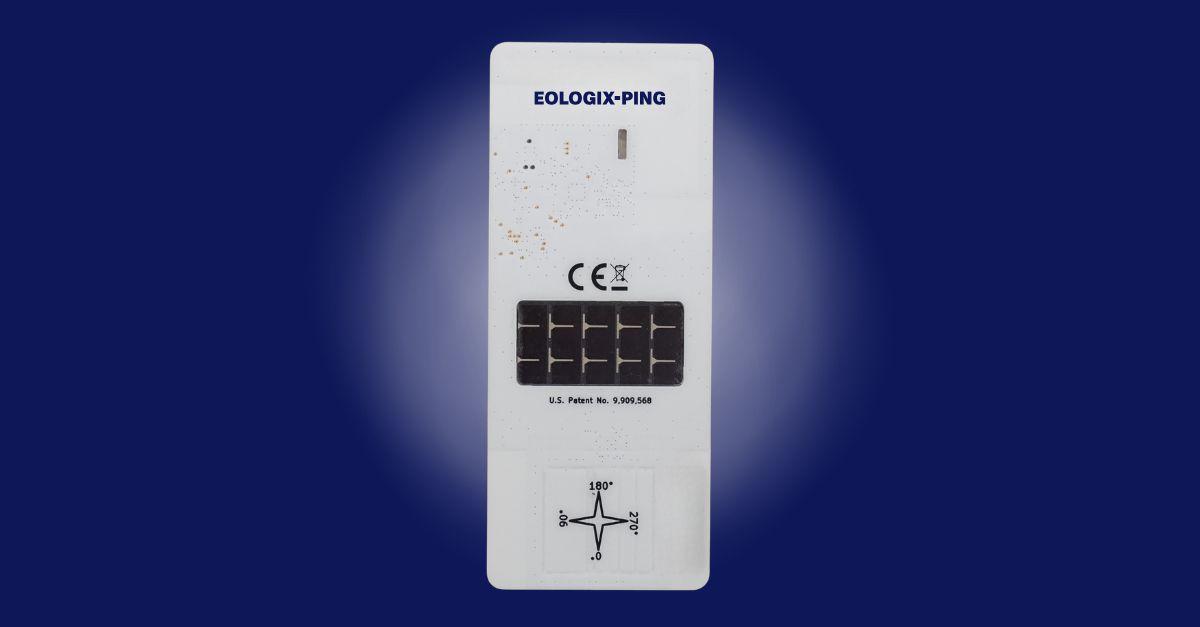
ON-BLADE system including temperature and ice detection sensors for efficient blade heating.
- Blade condition awareness
- Optimized starting and stopping of heating
- Dashboard access
- Training & Support
Cost Overview
Standard
:HEAT
•
High-precision ice detection for optimized blade heating
Package includes
This package contains Wireless Blade Sensors (WBS) and a Base Station.
:HEAT starting at
price per turbine in the first year
Any questions?
Reach out to us for tailored advice on your specific needs, to learn more about our technology, or to schedule a personal consultation. Our dedicated team is ready to assist you every step of the way.