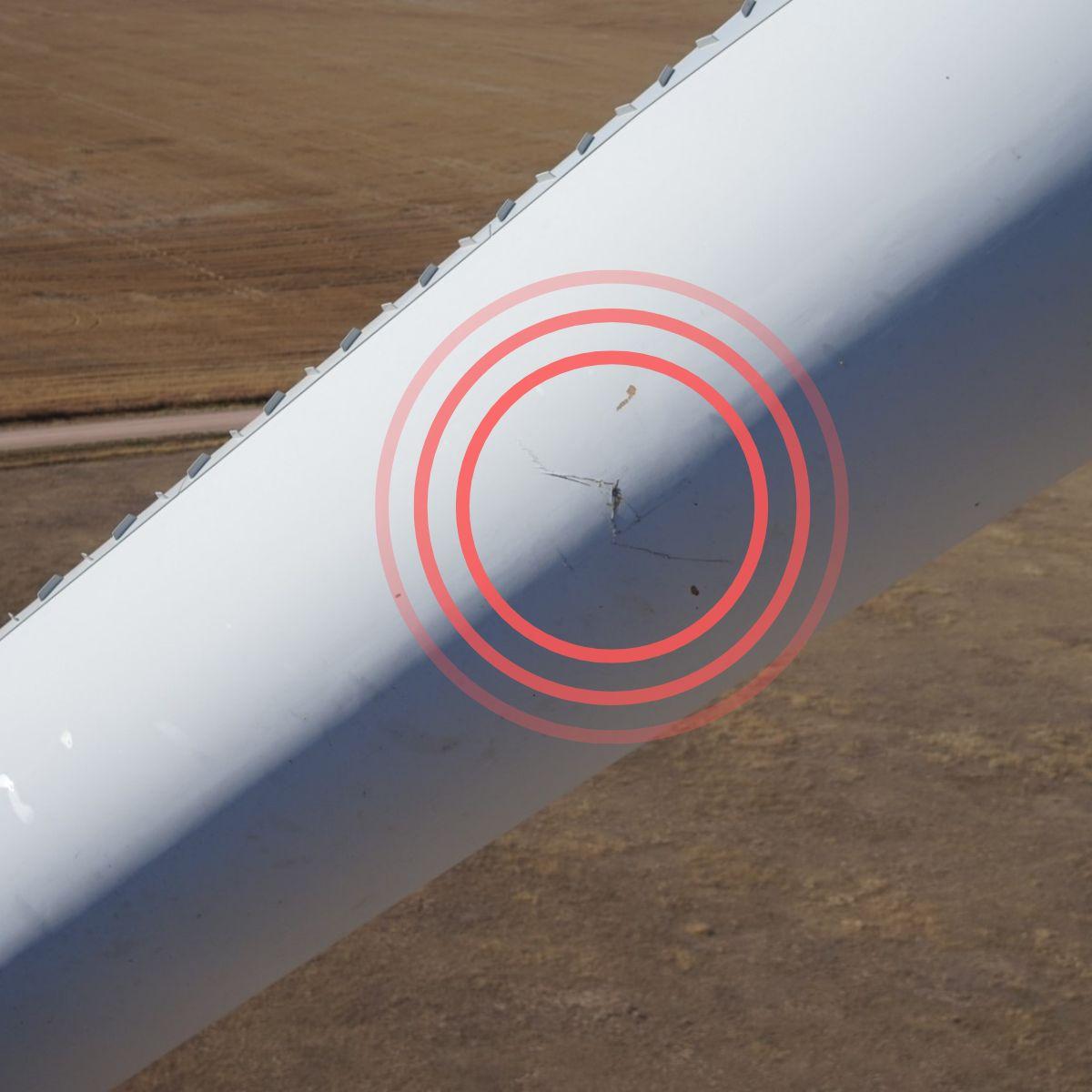
7 min to read
Detecting surface damage in wind turbines
Published: November 12, 2024
Updated: April 9, 2025
Wind turbines play a key role in the transition to renewable energy, but their performance can be severely impacted by a common, yet often overlooked, issue: Surface damage to the blades. Even minor erosion or cracks can lead to a significant reduction in energy output, higher maintenance costs, and unexpected downtime. For turbine operators, understanding the importance of continuous blade monitoring is essential – not just to prevent costly repairs, but to optimize maintenance efforts and control operational expenses.
Here’s why proactive surface damage detection is essential for controlling costs.
Why surface damage occurs and its impact on maintenance costs
Wind turbine blades are constantly exposed to environmental stressors. Lightning, strong winds, particulate erosion, and even cold-weather icing can deteriorate blade surfaces. Studies show that damage often accumulates on the tips and leading edges of blades due to high-speed impacts and natural wear. One frequent culprit is leading-edge erosion, which can reduce a turbine’s annual output by as much as 5%* if not addressed early.
Lightning strikes are another major source of damage, particularly affecting the blade tips. DNV considers lightning damage to be the single largest cause of unplanned downtime in wind turbines, which can quickly cause repair costs to soar. In many cases, repairs from lightning damage alone can exceed $30,000, excluding the potential revenue loss while the turbine is offline for maintenance.
The hidden cost of ignoring blade damage
Failing to address even minor damage early can lead to much more costly and labor-intensive repairs. Small cracks or delamination, when left unchecked, can escalate into major structural failures. Severe damage, such as blade tip separation or shell detachment, often requires the use of specialized equipment, including cranes, and can push repair costs beyond $200,000. What’s more, unplanned downtime due to extensive repairs means lost revenue—ranging from $800 to $1,600 per day.
Beyond the direct repair costs, unscheduled maintenance adds unnecessary complexity and effort to your operations. Not only do you have to contend with expensive parts and labor, but managing the downtime and logistics of turbine repairs can also take a significant toll on your resources.
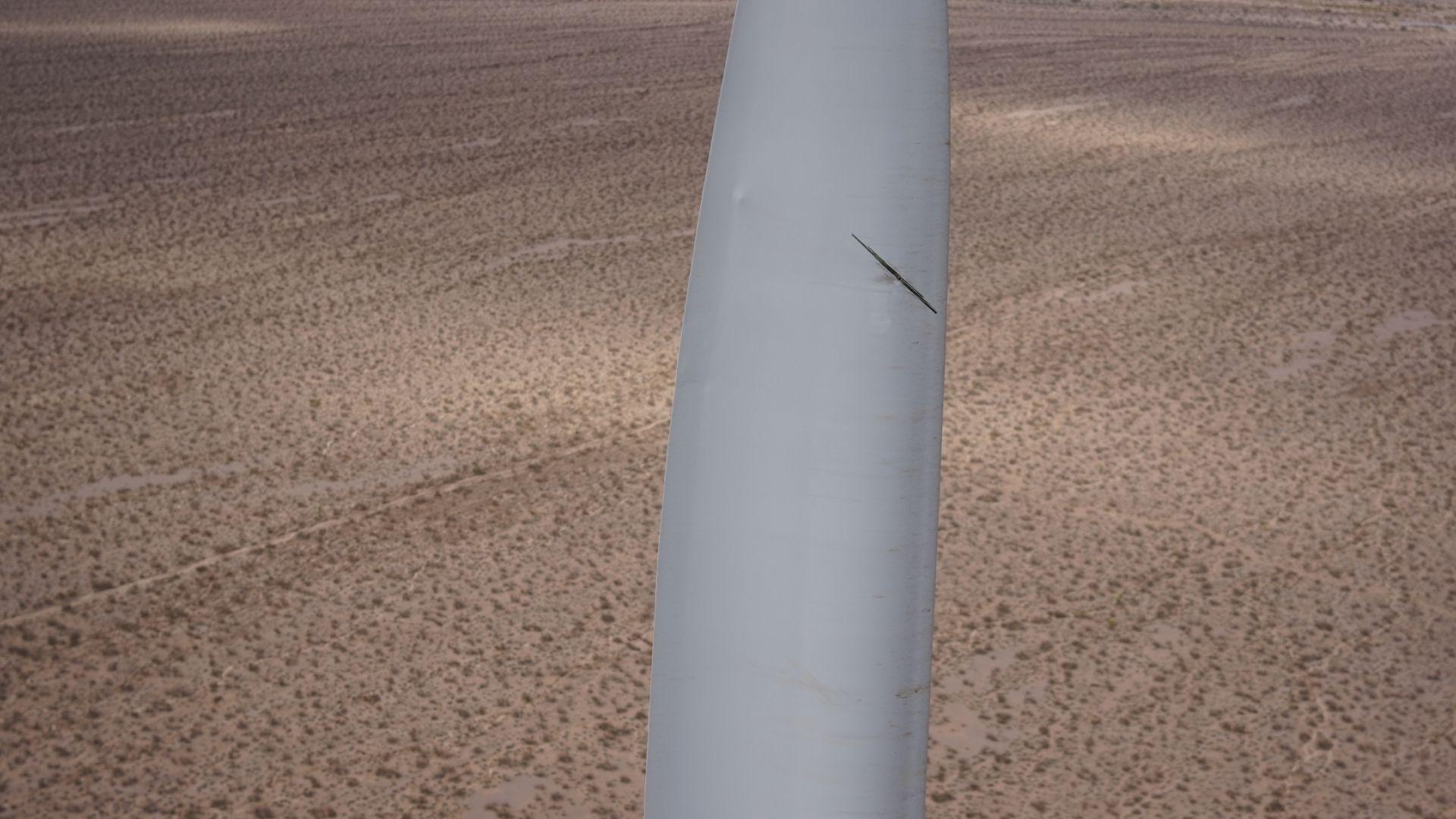
Want to learn more about damage detection? Download our whitepaper.
Copyright: SkySpecs
The benefits of continuous blade monitoring for maintenance efficiency
The solution to these escalating maintenance costs lies in early detection. Continuous blade monitoring with advanced technology, like acoustic sensors, allows operators to keep a constant watch on blade conditions in real time. These sensors detect surface damage as it occurs, offering a clear picture of blade health before issues develop into major failures.
By identifying damage early on, operators can carry out repairs during scheduled maintenance windows, reducing the need for emergency fixes and costly unplanned downtime. This proactive approach not only extends the lifespan of your turbines but also helps avoid the high costs and labor associated with major repairs, leading to significant savings in both time and money.
How EOLOGIX-PING can help you reduce your maintenance costs
At EOLOGIX-PING, we offer innovative acoustic surface damage detection and structural damage detection systems designed to minimize maintenance costs and effort. By continuously monitoring your turbines’ health, we help you spot damage before it escalates, allowing you to schedule repairs strategically and avoid unnecessary downtime. Our solutions give turbine operators the peace of mind that comes with knowing their turbines are operating at peak efficiency, reducing both the risk of major failures and the overall maintenance workload.
Interested in learning more about how our systems can help reduce your maintenance costs? Contact our sales team today for personalized guidance and find out how we can support your energy production goals.
Reference:
- Dimitris Al. Katsaprakakis, Nikos Papadakis, Ioannis Ntintakis (2021): A Comprehensive Analysis of Wind Turbine Blade Damage. MDPI, Basel, Switzerland.
- Imeson, A.C.; Vis, R.; de Water, E. The measurement of water-drop impact forces with a piezo-electric transducer. CATENA 1981, 8, 83–96.
Share this blog post
Get your blade damage whitepaper
How do you already know the condition of your blades? Find out everything you need to know about continuous blade damage detection, technologies and solutions for this sensitive topic.
Subscribe to our newsletter
Stay informed with the latest industry news, fascinating insights, and updates from EOLOGIX-PING delivered straight to your inbox.
PS.: We promise no spam.