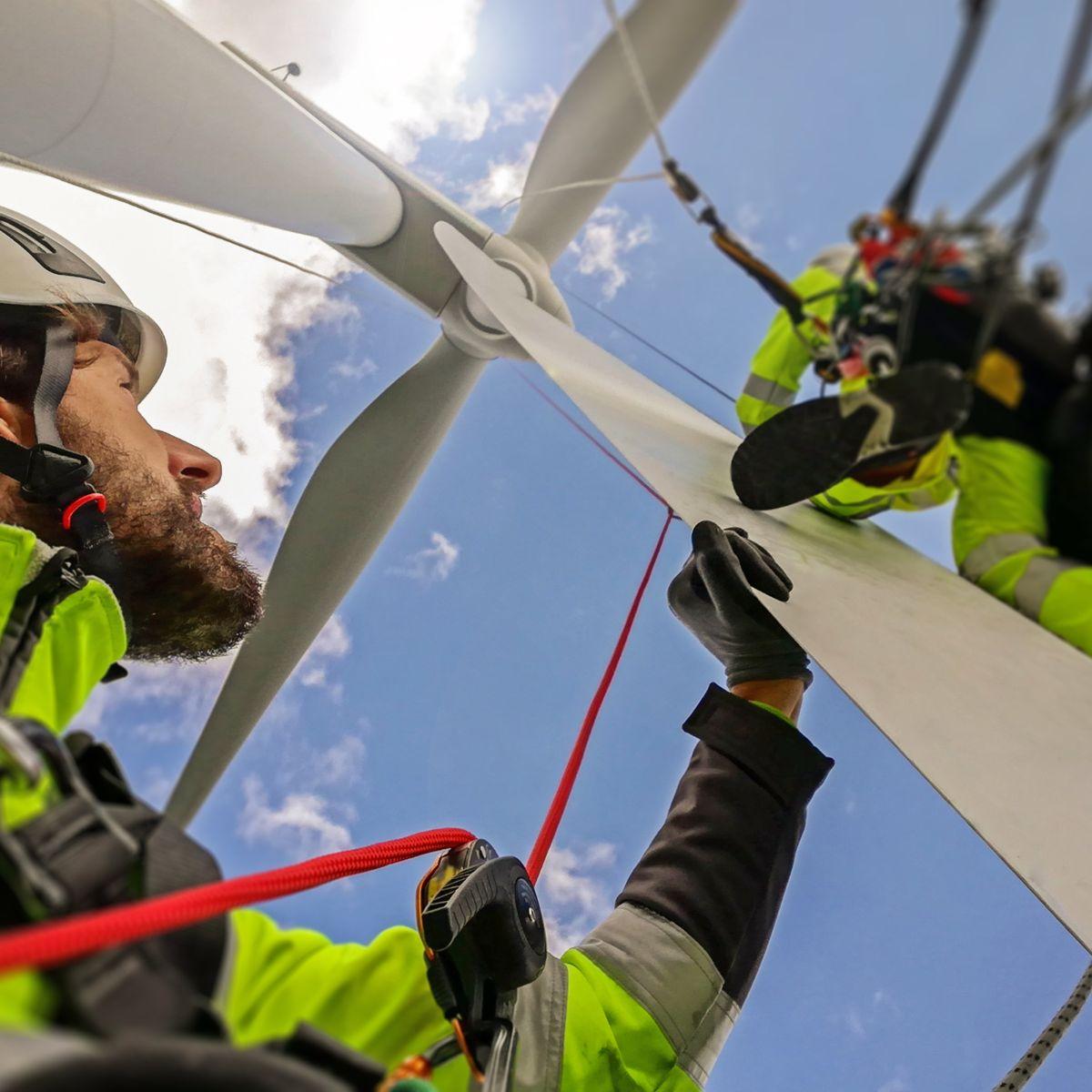
5 min to read
Challenges in blade monitoring for wind turbine operators
Published: May 6, 2025
Updated: September 4, 2025
Wind turbine blades are at the heart of energy production, and they operate under varying and often extreme conditions. From gusts, wake and shear to lightning strikes or ice buildup, countless stressors can affect blade performance and lifespan.
In this article, we explore the most pressing challenges in rotor blade monitoring and show how continuous sensor-based monitoring can help you reduce downtime, avoid costly repairs, and optimize your assets.
Why rotor blade monitoring matters
Wind turbine blades are designed to capture the wind’s energy efficiently. They are operating 24/7 in varying conditions and are exposed to stresses that can impact their performance and longevity. Without continuous condition monitoring, damage can go unnoticed until it leads to significant downtime or safety concerns. Understanding these threats is essential to proactive maintenance and long-term asset protection.
Stressors affecting wind turbine blades
Wind turbine blades face a wide range of challenges, amongst these are:
- Wind loads: Varying wind conditions cause material fatigue over time, especially turbulence intensity, veer and shear are contributing to fatigue loads.
- Temperature extremes: Sudden cold snaps, freezing winters or scorching summers introduce thermal stress, increasing the risk of cracks and delamination.
- Moisture and ice: Ice formation reduces aerodynamic performance, causes imbalance, and can damage internal structures.
- Debris impact: Hail, salt and dust can erode the blade surface and lead to microcracks.
- Operation: Relative blade angle differences due to installation or commissioning mistakes can cause aerodynamic imbalance which can lead to increased stress of blades and other turbine components.
- Manufacturing limitations: Sometimes, invisible defects occur during the manufacturing process, such as weak spots, wrinkles, or imperfect bonding of materials. These issues may not show up right away but can worsen over time, especially under high stress or repeated use, eventually leading to cracks or breaks in the blades.
- High stress concentrations: Areas with high stress, such as holes and notches, can be more susceptible to cracks.
- Handling damage: Transportation and installation errors can lead to structural weaknesses before the turbine even starts operating.
These challenges highlight the need for early damage detection and reliable monitoring solutions.
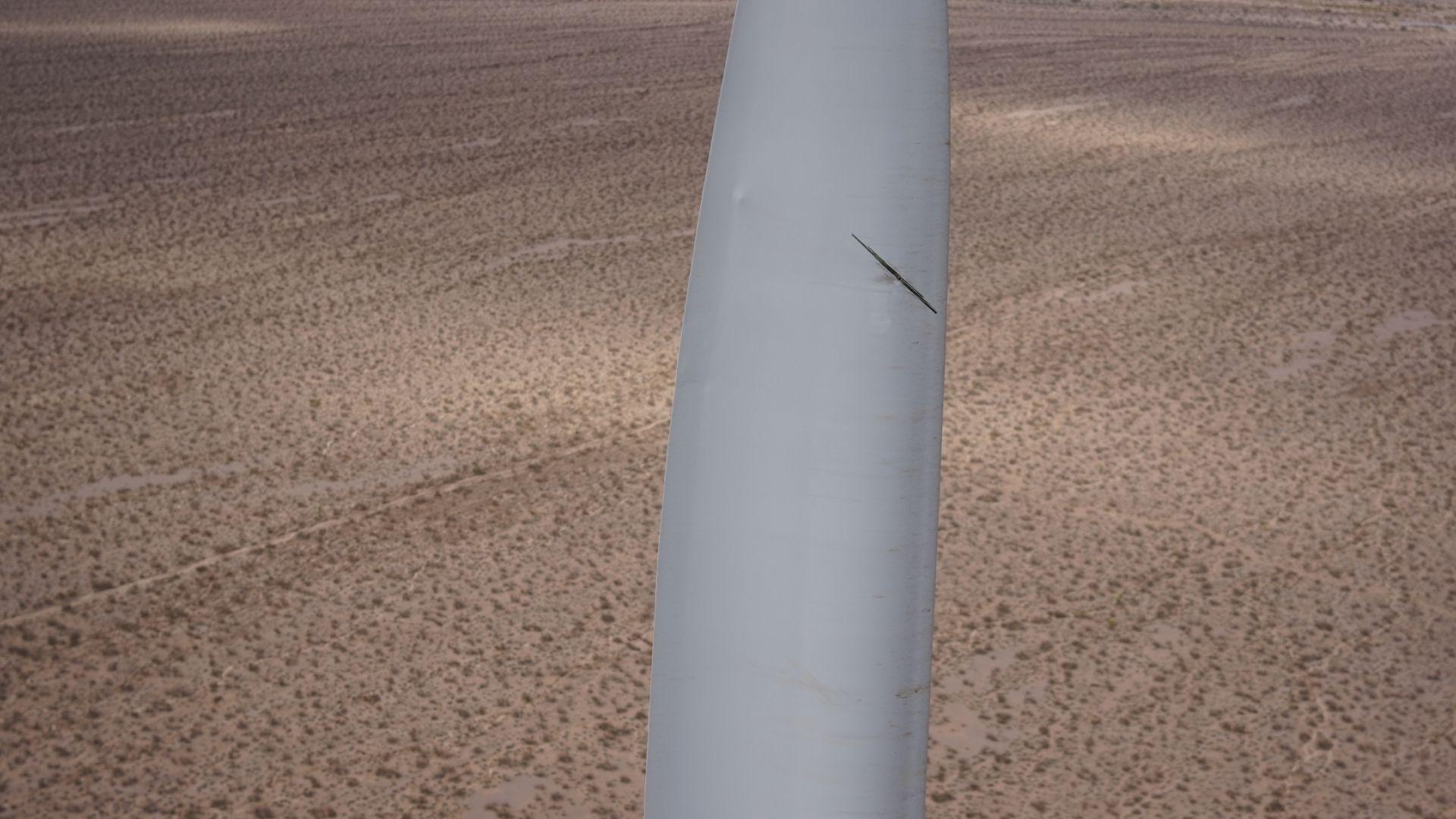
Want to learn more about damage detection? Download our whitepaper.
Copyright: SkySpecs
Common types of rotor blade damage
Several forms of damage can affect rotor blades, some visible, others hidden deep inside:
- Lightning strikes: Lightning strikes are the number one cause of blade failure*. The tall structures of wind turbines can attract lightning strikes during thunderstorms or winter season. Upward lightning is particularly dangerous and difficult to identify for Lightning Location Services (LLS).
- Erosion: Erosion or leading-edge erosion occurs due to the impact of weather and airborne particles such as sand, rain, or hail but can also be caused by exposure to moisture, saltwater, or chemicals in the environment.
- Surface cracking: Cracks mean structural weakness developing over time**, caused by mechanical stresses or UV exposure. It can grow into deeper cracks, affecting the integrity of your assets.
- Transportation damage: Transportation damage may be caused by wrong handling, lifting, and road vibrations***.
- Debonding: Debonding means the adhesive failure between the layers, resulting in structural failure.
Even seemingly minor flaws can snowball into severe repairs if left unchecked. According to the experts from Weather Guard Lightning Tech, Allen Hall, Rosemary Barnes, Joel Saxum and Philip Totaro, lightning damage and root cracks alone cost the industry hundreds of millions of dollars annually****. Understanding these root causes is essential for operators to anticipate potential risks and ensure timely repairs.
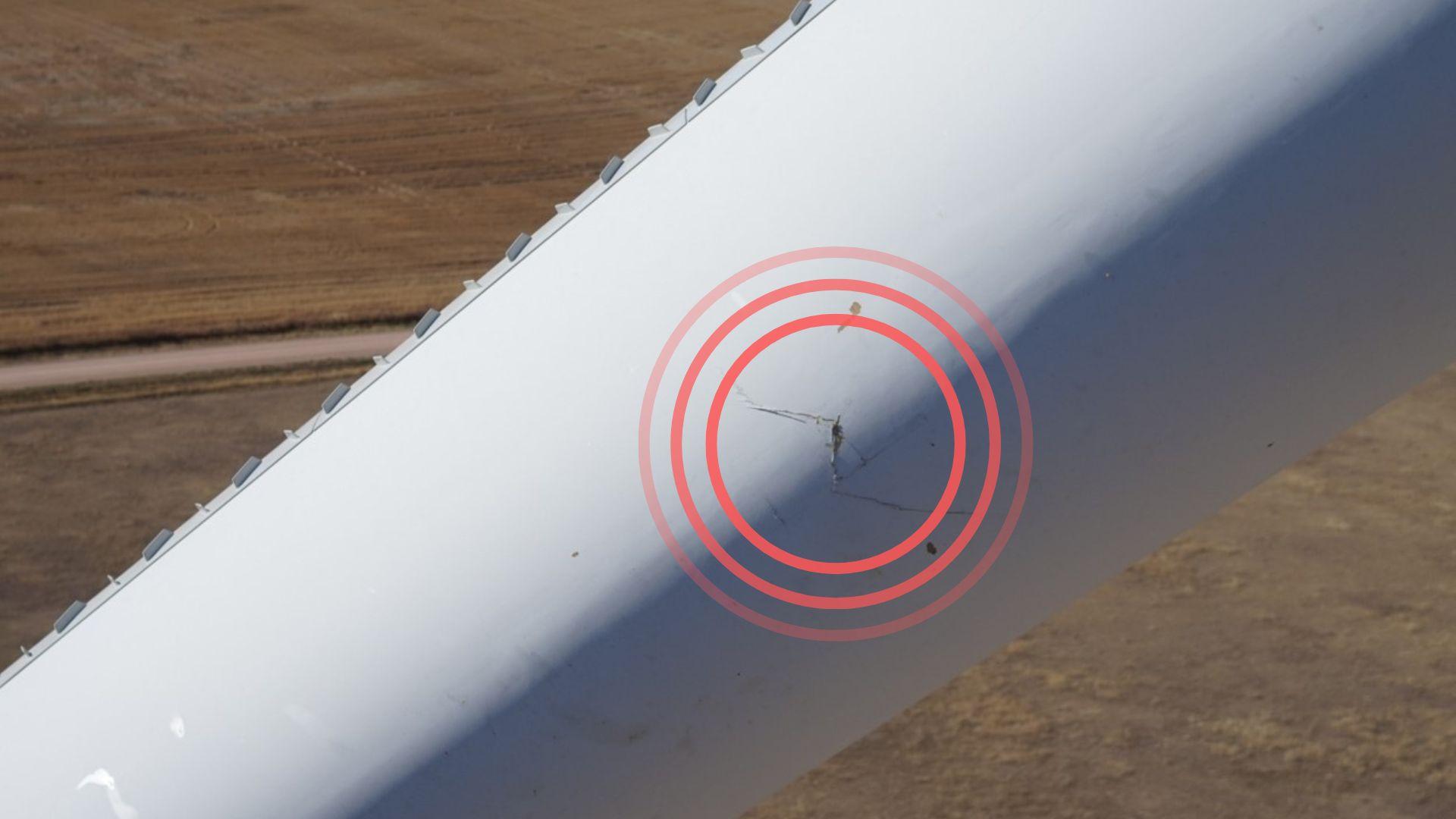
Surface damage detection for wind turbine rotor blades.
Consequences of untreated blade damage
Failing to identify blade issues early can result in:
- Highter maintenance costs: Undetected damage can escalate into more severe problems requiring extensive repairs or even blade replacement. This results in increased maintenance costs and extended downtime.
- Safety concerns: Severe blade damage can compromise turbine safety, posing risks to maintenance personnel and nearby equipment. Ensuring blade health is essential for maintaining a safe working environment.
- Operational disruptions: Large intervals between inspections can lead to unplanned maintenance and operational interruptions. This affects the ability to generate consistent energy and meet production targets.
- Reduced energy yield: Damage can reduce aerodynamic efficiency, leading to lower energy production. This impacts revenue as well as overall profitability.
Harsh environmental conditions accelerate blade wear and tear, often making damage difficult to detect. With varying inspection frequencies across wind farms, there are significant risks of undetected damage leading to costly repairs and extended downtimes. This makes continuous blade monitoring for wind turbines essential, not just for safety, but also for maximizing return on investment.
The value for operators
Continuous monitoring throughout the year is crucial for detecting damage at an early stage and initiating appropriate measures. It supports operators to:
- Perform triggered inspections instead of costly periodic checks, allowing operators to optimize maintenance planning and reduce unexpected downtime.
- Track the progression of blade damage and signals when repairs become urgent, which is useful for severe blade damage scenarios or when labor/budget constraints limit periodic inspections.
EOLOGIX-PING offers multiple solutions for continuous monitoring, from surface and internal blade monitoring to lightning and ice detection – just like how your monitoring needs can range from a quick status check to an in-depth performance analysis!
References:
*Garolera, A.C., Madsen, S.F., Nissim, M., Myers, J.D., Holboell, J. (2016): Lightning damage to wind turbines blades from wind farms in the US. IEEE Transactions on Power Delivery, 31(3): 1043-1049. https://ieeexplore.ieee.org/document/6966755
**Zhou, Q.; Liu, C.; Bian, X.; Lo, K.L.; Li, D. (2018): Numerical analysis of lightning attachment to wind turbine blade. Renew Energy, 116 Pt A, 584-593.
***The Energy Mix: ‘Substantial Damage’, No Injuries as Freight Trains Hits Wind Turbine Blade. https://www.theenergymix.com/substantial-damage-no-injuries-as-freight-train-hits-wind-turbine-blade/
**** Uptime Wind Energy Podcast of Weather Guard Lightning Tech “How Low Cost CMS Stops Catastrophic Damage”. https://www.youtube.com/watch?v=HmfIpzvhcPM (04.03.2025)
Share this blog post
Get your blade damage whitepaper
How do you already know the condition of your blades? Find out everything you need to know about continuous blade damage detection, technologies and solutions for this sensitive topic.
Subscribe to our newsletter
Stay informed with the latest industry news, fascinating insights, and updates from EOLOGIX-PING delivered straight to your inbox.
PS.: We promise no spam.